Prebuilding a custom yacht through mock-ups
by Lyman-Morse Boatbuilding 1 Nov 2019 07:46 PDT
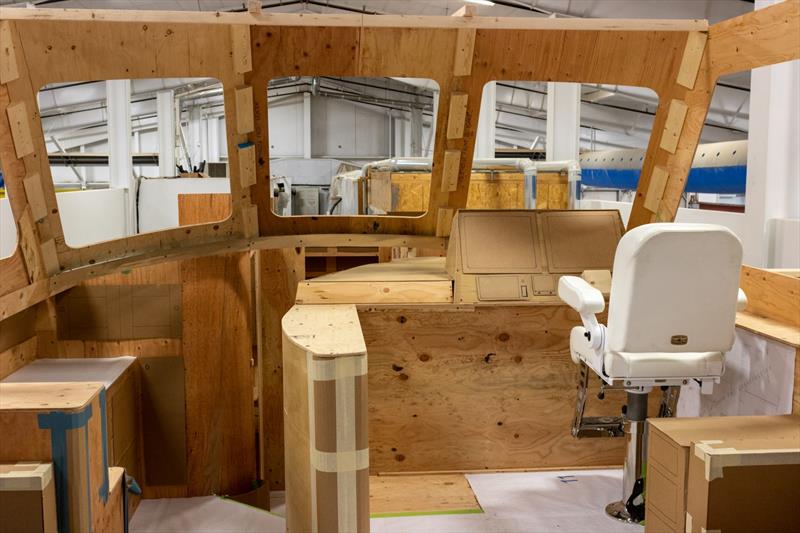
Hood 57 mock-up © Lyman-Morse Boatbuilding
Lyman-Morse operates in the rarefied air of custom boatbuilding. We have spent decades visualizing sailing and power yachts from the blueprints, and now computer screens, in design offices around the world. But for our clients who step up to bring one of these visions to reality, we have found that a little "virtual reality" can ease the breathing at this altitude. No, we don't have a Star Trek holo deck in Thomaston (not yet, at least) but we do the next best thing. We build a mock-up. That is, Lyman-Morse has found it pays to produce an exact, full-scale model of a one-of-a-kind boat before it ever gets built.
"This is not a new practice for us," says Drew Lyman, president of Lyman-Morse. "We find it is incredibly helpful in the design phase for customers to literally walk through the project."
"We are used to looking and working with blueprints and 3D models, but for most of our customers, this is the first custom boat they have built and we want them to have the greatest comfort and understanding of the project. It's way better for everyone to make changes in the mock-up stage."
So it was, over the past year, that Lyman-Morse Boatbuilding created the full-scale walk-in diorama of the deck, cockpit and interior volumes of the new Hood 57, currently under construction at the Thomaston boatyard. What's needed for a mock-up? Enough 1/2-inch plywood, cardboard, masking tape, hot glue, and Magic Markers, plus two carpenters who spend about two weeks building the full-scale version of the vessel from plans, data files, and instructions supplied by the boat's designers. Skill and cutting-edge techniques are involved, but making full scale marine mock-ups is also an intuitive process. "There is no stress. It is like putting together a tree house. But the level of detail is cabinet grade," says Ken Overlock, a carpenter who, along with Pat Flynn, made up Lyman Morse's so-called Mock-Up Squad over this past winter.
Setting up the Mock-Up
For the mock up of the custom 57-footer the two built this past winter on the third-floor mezzanine of Building 11 on Lyman-Morse's Thomaston campus, the full-scale, carefully indexed and marked floor plans were printed in-house on 3-foot-wide translucent Mylar rolls. Overlock and Flynn then carefully laid out these up to 20-foot-long templates; and over the course of about two days, a full-scale floor plan of the yacht featuring basic elevations, came to life under the duo's feet.
"All the interior volumes and furnishings were there: The beds, the tables, and chairs," says Overlock. "It begins to feel like a real boat."
The Computer-Generated Mock-Up
Next, Lyman-Morse's CNC shop shaped full-scale plywood cut-outs of the bulkheads and vertical elements of the 57-footer. This Ford 150 pickup-sized stack of plywood shapes included perfectly accurate forms for doorways, cabinets, and other athwartship features. Just as the build team will do when constructing the actual boat, the Mock-Up Squad hangs reference blueprints on the wall. Those plans were the critical guides the duo used to match the plywood cutouts to their proper locations on the Mylar floor plan.
"The components from the CNC are numbered to the plans," says Flynn. "Then we fleshed all that out with the other materials and brought everything into 3D."
Cardboard is an excellent proxy for complex composite hull shapes. Tape and glue played the role of marine fasteners. Cheap plywood was the stand-in for exotic hardwoods. And the Magic Markers? They marked the faces of the cabinets, drawers, and computer screens.
Test Driving through Mock-Ups
Overall, the goal was to make the mock-up experience as close to the finished boat as possible. That way, the customer can walk through, lie down in their stateroom, confirm closet and storage space, sit in the helm seat, move around the passages, check out the efficiency of the galley, and imagine the coastline sliding by while seated in the pilothouse. The design and boatbuilding team is there to get the feedback and make adjustments if needed. For instance, in the case of the 57-footer, the flybridge stairway was adjusted to accommodate taller people.
Though both Flynn and Overlock chuckle when teased about working with "marine-grade cardboard," both were impressed by how the design team harnessed the CNC machine, Mylar printer, and other tools to create an accurate rendering of not only the look, but the feel, of the boat.
It is an extra step, but all this makes for a better experience for the owner and his entire boatbuilding team.