Under the skin of the J/112E
by Mark Jardine 4 Nov 2023 01:00 PDT
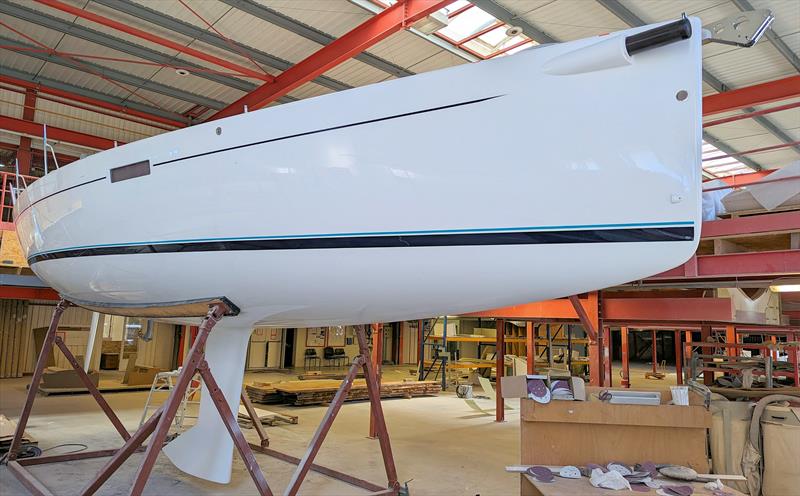
J/112E in build at J Composites © Mark Jardine
What happens under the layer of gelcoat on a yacht is inherently invisible to the naked eye. At a boat show what you see is the shine and the shape, the glitz, and the glamour. The yachting lifestyle is demonstrated to you in all its glory, with photos and videos of glorious days on the water, lapping up the sunshine with idyllic beaches in the background.
Making the best of your time on the water is an absolute priority for most, and being able to cruise comfortably at a decent speed to a favourite destination will be high on any prospective yacht owner's list, and obviously you'll want a yacht that lasts the test of time, is light and airy, and is a joy to sail.
For a company such as J-Composites, combining these requirements has always been the objective. With a strong racing heritage, they're masters of performance construction and are known for attractive yachts with superb hull forms. Their cruising yachts combine all the comforts you'd expect, but without compromising on making the sail from A to B a joy, and at good speed.
To achieve this J-Composites have chosen not to take the easy path on construction, as I found out when I travelled to Les Sables-d'Olonne in France, the town which famously hosts the start and finish of the Vendée Globe, to tour the yard with Frédéric Bouvier, their Commercial Manager.
We first went to the marina in Les Sables to take a look around a J/112E which an owner had been sailing since May. The immediate feelings on board are that of space, simplicity, and elegance. The combination of an airy saloon and relatively wide side decks meant that straight away I had questions about how they achieved this balance. The front bulkhead is well forward of the mast (which is pleasingly central in the dining table) and had me fruitlessly searching internally for the stringers from the shroud chainplates. The large coachroof windows, the high internal headroom and the generous companionway all made me want to discover the structure's secrets. I needed to get under the skin of the J/112E, and thankfully I was in exactly the right place to do so.
One of my favourite positions on board was the forward-facing chart table, which had an open-plan office feel to it. It would be so easy to combine a bit of morning work on board a yacht while still being able to join conversation with crewmates. Modern life means you can stay connected while out and about, should you so wish, and the ability to do so in a relaxed and comfortable manner felt very right.
We departed the marina and made the five-minute drive to the J-Composites yard. Seeing yachts, and their many component parts, in various stages of construction, gave me a superb insight into the 'how' and 'why' thoughts on the J/112E construction which were running through my head.
First up we took a look at a freshly laminated hull with the 'grid' in place. While this immediately answered one question, as I saw the unidirectional glass around the bulkhead and chainplate areas, which provided the strength and rigidity needed, it brought up another question: Why the balsa wood? Surely foam-sandwich construction is preferable? While foam is used as well (the green areas in the photo above), all the areas with greater curvature were balsa.
Frédéric gave me a great demonstration as to why the combination is better by laying two foam and balsa sections side-by-side. The foam is CNC-cut, so there are small gaps between each square, whereas the balsa is cut into pieces and then bonded to a backing fabric, eliminating the gaps. On curved areas this dramatically reduces the amount of resin that is needed. While foam is lighter than balsa, the reduction in resin used vastly outweighs the difference, and balsa is also less susceptible to compression.
Foam still has its place, and is used extensively as well, especially on the deck mould where there are fewer curves, and you can make it thinner. Hard points, for example where the jib track and padeyes are sited, use a harder foam to handle the compression loads.
The grid structure, like the hull and deck, is vacuum-infused, which is the best method for ensuring even and air bubble-free resin impregnation, using the minimum amount of resin. By a long shot it's not the easiest technique, and requires considerable skill and knowledge, but that's where J-Composites racing pedigree comes in handy.
As Frédéric explains:
"There are three advantages of vacuum-infusion: the first is the compression of the layers of fibreglass together, which gives better attachment on every layer, the second advantage is the lower ratio of resin to fibreglass and other structures, leading to a ratio of 70% structure and only 30% resin (any more resin doesn't make a structure stronger, just heavier). Finally, the vacuum process removes all the air, even the micro-blisters from the structure, so the connection is 100% everywhere, which further prevents delamination."
As a cruising sailor, and talking about a cruising yacht, you may be wondering why these technical details are important. By making a hull lighter and stiffer, weight can be transferred to the keel, and a lighter hull, with lower wetted surface area, is easier to drive, which means less sail area is needed, with correspondingly lower sheet loads.
The increased speed and ease of use increases range, opening up new cruising grounds for weekend sailors and bluewater cruisers alike, not to mention the sheer joy of the sailing itself.
The wiring loom and piping is all fitted inside the grid before it is bonded into the hull, ensuring it's all out of the way, as well as being central and low in the boat. So much of the J/112E construction demonstrates how performance and space considerations can work in perfect harmony.
The hull mould is in two parts, divided down the centreline. After the gelcoat, lamination work starts with the strong points of bulkheads, chainplates and the windows, moving onto the deck join curve, and then joining the two parts before laminating the centre of the boat.
All through-hull fitting positions have a silicon mould inserted in them, so that the gelcoat and fibreglass is shaped around the fitting. It would be simpler to just drill through the hull during fit-out, but that would leave exposed fibreglass on the side of the fitting.
The deeper you look, the more you find out the details on the J/112E, and the deck mould includes the deck grip, so this is built into the gelcoat rather than painted on. It's another complex process, as ensuring the deck then releases from the mould is trickier when you have an inherently rough surface, but it's more evidence of J-Composites' uncompromising approach.
There's no better demonstration of the stiffness build into the deck than when it's being fitted out prior to being bonded to the hull. Very few props are needed, and there is so little flex.
This monocoque construction is of huge advantage for the cruising sailor. By transferring the loads throughout the hull and deck, there are no structural beams in the main salon, and the large windows makes the feel the interior feel remarkably light and airy.
The carpentry is all done at J-Composites, which includes a range of solid wood and laminates, again striking the balance between aesthetics, weight, and cost. The team carefully select the wood so that the same grain and colour is attained throughout any one yacht, with veneers and solid wood components cut from the same section.
Attention to detail and design philosophy were again evident on the laminating, with the top veneer cut short of the edges on the wooden aft bulkhead, so that the fibreglass bond between hull and bulkhead is as strong as possible, while reducing material needed. Weight reduction, increasing strength and maximising space working in perfect harmony.
Frédéric concluded the tour by saying, "the devil's in the detail," and I wholeheartedly agree. It's the combination of hundreds, if not thousands, of tiny design and construction elements which come together to make the J/112E what it is. These details can be devilishly difficult to achieve, and require a highly skilled workforce, but the end result is, quite simply, astounding.